“Had the diameter of the space been a couple of millimetres larger, our disc spring pack would have produced a force of 400 Newtons.”
There are numerous different standard springs for different uses, for example, for valve manufacturers, trailer industry, elevators, and process industry. It is essential to always find the most suitable solution for the challenge at hand. As a rule of thumb, the greater the need for power, the shorter the travel. In a traditional coil spring, the round steel wire is the starting point. It is followed by square wire and tool springs, before we arrive to disc springs and disc spring packs.
There are many dimension and raw material options available. You can find the most preferred and common of them in our Spring Store; the rest are conveniently and readily available through our comprehensive partner network.
The direction of the force is also of great importance. In general, springs are divided into compression, extension and torsion springs. A major part of the function of a extension spring, in other words, tension, can also be produced by other springs, which provides alternatives for an optimal solution. This is not necessarily of general knowledge.
In case of coil and tool springs, the force produced can be calculated in Newtons per millimetre (N/mm) of compression. In case of disc springs, compression amounting to tens of thousands of Newtons can be achieved with just a few millimetres of travel. When it comes to disc springs, we use the most suitable ones based on the need and specifications – from entry-level products all the way to Mubea springs of the highest quality.
Space is the greatest limiting factor
In case of almost every challenge in our spring design, the need for, and amount of, space define the limits for the solutions. In one of our example cases, the maximum possible spring force was pursued in a specific limited space: 6 millimetres in diameter and 15 millimetres in height. We managed to achieve 62 Newtons with a coil spring and 209 Newtons with a mini-series tool spring. Had the diameter of the space been a couple of millimetres larger, our disc spring pack would have produced a force of 400 Newtons.
The example above is a typical situation where springs have not been considered sufficiently in the overall design. Had the space been slightly larger, we could have doubled the force by using disc springs.
“As our customer, you need not know the best solution. It is our job.”
Involvement in the design as early as possible
In the design phase, the issue in the example above could likely have been resolved with a minor modification, whereas any changes made afterwards result in additional work steps that always come with a price tag. The best results are almost without exception achieved through early co-operation in design. As our customer, you need not know the best solution. It is our job. You only need to tell us the challenge that needs to be solved. In addition to the force and space required, challenges may be related to temperature or the travel of the spring, for example.
Through co-operation in design, we can also significantly affect the carbon footprint of production and of our customers’ products by reducing the number of work steps in advance. The materials used for spring manufacture are utilised almost one hundred per cent and hardly any waste is generated. Furthermore, spring steel is well suited for recycling when the spring reaches the end of its service life.
Tell us your spring challenge and we’ll find a solution!
Markus Jokinen
Business Unit Director, Springs
+358 40 827 3289
Pasi Suvela
Product Manager, Vantaa
+358 40 668 1832
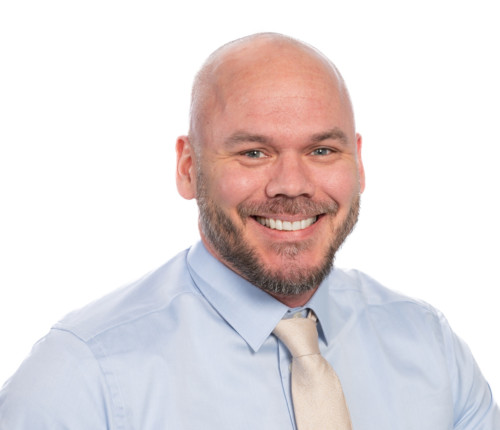
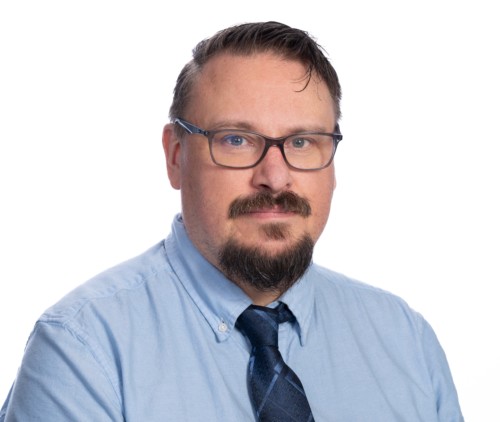
Download spring design tips
Consult the Meconet Spring Design Guide for help. We put together tips on how to design the perfect coil spring.
Read more