With regard to spring design and manufacturing, we work closely together with the client in order to achieve the best possible result for them. Of course, this is something we always aim for, but I thought I would write about spring-related challenges regarding weapon-making in particular. These products are typically used for recreational, competitive or government purposes, so above all, they must be safe and reliable. The starting point for everything is product safety and reliability.
Tremendous strain on a spring in a weapon
Typically, weapons are valuable and long-lasting, with a lifespan often reaching several decades. That poses challenges for the spring. In weapons, the mechanisms can be very challenging and critical for the end product.
A compressed spring is typically subjected to strain, which the spring has to withstand for several years. The number of repetitions can be enormous, and this strain must be taken into consideration in different ways in the weapon spring design. Furthermore, movements using the weapon spring can be very fast. Weapon mechanisms generally also require several springs to work together. It is not enough to check the tolerances of just one spring, for example; instead, wider tolerance chains must be taken into consideration, consisting of other springs and the surrounding parts. Managing these tolerance chains requires the manufacturing process to be as precise as possible.
In weapons, the usability of a product is at least as critical as tolerance chains. Pressure is always generated when firing a weapon. For a weapon to withstand it, it must be made from high-quality steel. However, for weight reasons, the amount of steel is minimised, typically making the space reserved for the spring small and cramped. Therefore, the spring must be able to work as required in the smallest possible space throughout its entire lifespan.
A high-quality spring is carefully designed and manufactured
We have the necessary know-how and methods to meet even the most challenging spring requirements. With pre-stressing, we can increase the spring wire’s yield strength and relevant spring characteristics, so that the spring is more durable even in tight spaces. With shot peening, we can get the desired tension throughout the entire spring surface, as well as eliminating any deficiencies, such as scratches, which are the least durable parts of a spring. This method significantly improves the dynamic durability of the spring.
At Meconet, spring coil automation lines have a 100% camera vision inspection system; so only the best springs are manufactured. Spring designers must be experienced and achieve theoretical calculation results that are as effective as possible. Quality manufacturing does not cover up design errors.
A handgun is typically subjected to 15,000 – 20,000 operating cycles during its lifespan. With use, the spring begins to shorten and lose its strength over time. After a certain time, the spring will become so loose that the weapon can no longer fire. This characteristic cannot be eliminated from the spring, but good design can minimise it – at best, the effect will be insignificant for the final product. When the design and manufacturing process are completed well, the springs and the end product work in the desired way as long as possible.
Exceeding customer expectations
A few years ago, we were approached by a pistol manufacturer who was in the middle of designing two new pistol models. Both of these models required two springs, and the previous spring manufacturer clearly struggled to provide sufficiently good design and functionality. The quality and functionality requirements were not met. This was the starting point of Meconet’s collaboration with the client.
First, the client defined the required functionality as well as the space and the surroundings of these two springs in the weapon. The client had skilled representatives in the design process, we were able to obtain information and limit values for functionality, enabling us to complete spring calculations and simulations quickly.
After the first stage, our spring design was already complete, and we moved on to the prototype stage. After a few prototypes, we managed to manufacture springs for two pistols that exceeded all customer expectations. Now, the pistols are entering the serial production stage, and the client is expecting these new products to be received well on the market.
This project was great practice for the client and Meconet, as both parties could contribute their specialised skills to achieve a result that would have been unobtainable working independently. The best kind of collaboration – innovations are built together!
Do you want to hear more about spring design? Download our guide!
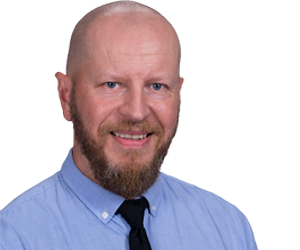
Download spring design tips
Consult the Meconet Spring Design Guide for help. We put together tips on how to design the perfect coil spring.
Download