Meconet is a North-European manufacturer of high-quality deep drawing panels for forestry harvesting vehicles, off-road vehicles, and various other applications, serving clients like AGCO, John Deere, and Mitsubishi Logisnext. The company provides the tools these OEMs need to deep draw reliable sheet metal parts.
Meconet upholds its motto, “Innovations are built together,” by collaborating closely with customers throughout their journey, from design to serial production. Simulation plays a key role in supporting tool design and analysis to achieve their objectives.
Simulation at Meconet: A Historical Perspective
Two decades ago, Meconet followed industry norms, relying on the expertise of deep drawing professionals to design high-quality tools. They came up with a basic design and gradually refined it through trial-and-error loops. This process was time-consuming and costly, requiring significant resources to achieve satisfactory results.
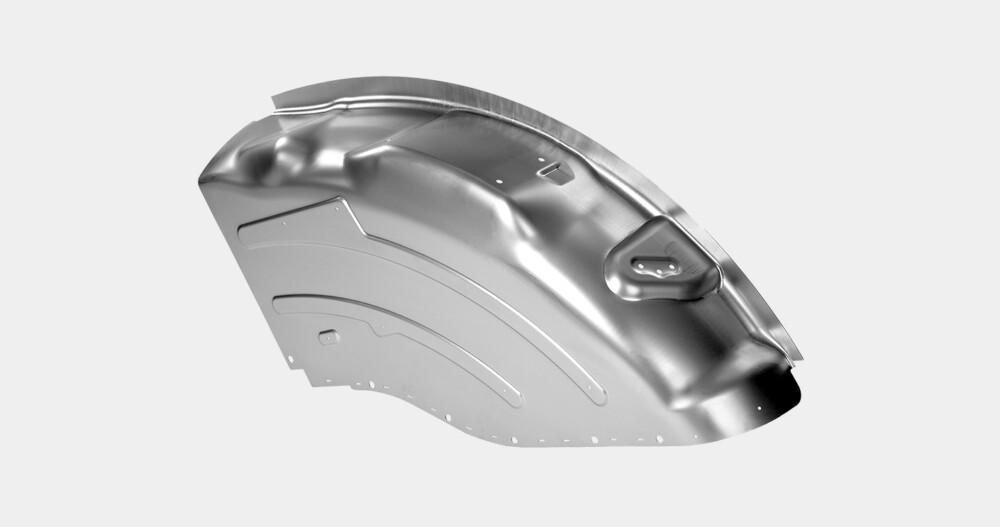
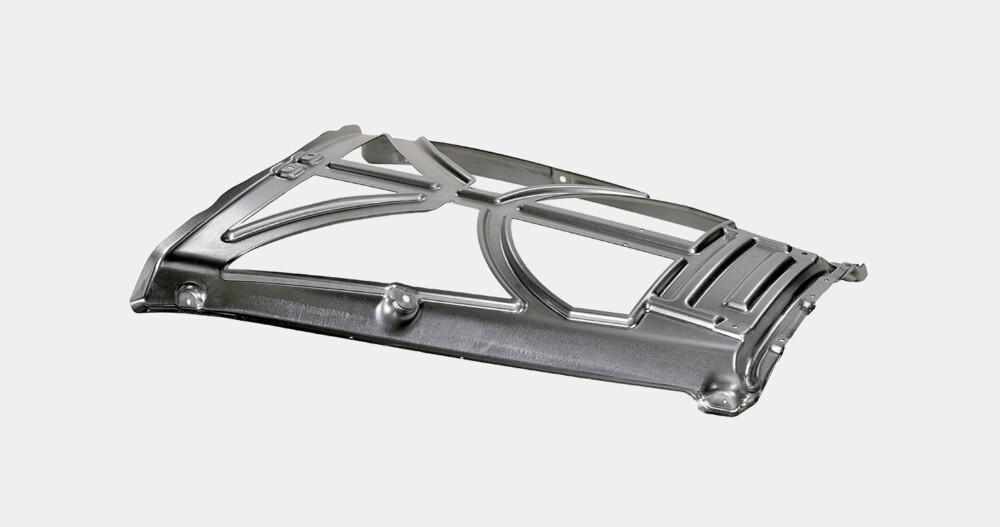
This method changed in 2004, when Meconet began using deep drawing simulation software to enhance the quality and efficiency of its stamping tools. They became one of the first companies outside the automotive industry to experiment with deep drawing simulation. Today, Meconet works closely with customers from part design through installation, ensuring the superior quality of their deep drawed parts.
“Simulation is an essential part of the process at Meconet today”
Juho Pirnes, Engineering & NPI Manager at Meconet.
The Role of Simulation at Meconet
Simulation is now integral to Meconet’s process. They begin by assessing the feasibility of aligning the customer’s design with their desired objectives. For example, if the customer wants to deep draw the part using a single tool, Meconet engineers analyze the design and collaborate with the customer to ensure that one tool can deep draw the entire part.
Underscoring their motto, “Innovations are built together,” Meconet’s design and tryout teams work closely with each other and with the customer. This collaborative approach breaks down the usual silos for a well-designed process delivering high-quality parts within the specified timeframe. Currently, the company uses simulation for deep drawing aluminum, HSS, and stainless steel.
Meconet offers comprehensive in-house capabilities, including sheet cutting, deep drawing, 3D laser cutting, mechanical cutting, washing, robotic welding, and riveting operations. They use simulation tools for parts ranging in size from small components up to very large 3000mm deep drawing parts.
Advantages of Simulation Integration
Simulation has played a pivotal role in Meconet winning numerous bids and consistently meeting or exceeding customer deadlines. Specific advantages include:
1. One-stop shop for all deep drawing needs
Customers now have a single partner to assist them throughout their entire journey, from design to serial production. Meconet helps with designing tools based on part geometry, collaborating on modifications, and designing the process and tooling. The tools are then installed in Meconet’s production for a seamless customer experience.
2. Reduced tooling costs
Naturally, customers want to minimize the number of tools required to produce the final product from the blank to save costs, particularly for low and medium volume production. If possible, they also want to minimize the number of parts while maintaining the same function. This also eliminates additional processes like welding and eases assembly.
Simulation enables Meconet to excel in this area compared to their competitors, consolidating multiple parts into a single deep-drawn part, which can also be deep drawed using a single tool. This streamlines production to a draw die stage followed by laser trimming for a finished part.
In one instance, Meconet reduced the number of parts for a French customer from seven to just one. The customer has since become a repeat client of Meconet.
3. Laser cutting advantages
While laser cutting may not be as cost-efficient in the automotive industry due to high volumes, it can be used effectively in industrial applications with lower volumes. Meconet effectively integrates laser cutting in its processes due to the reduced number of parts and overall production volume. They can program, fix, and laser-cut any shape they need, requiring only a single laser trim to achieve the final part after the drawing die stage.
“Meconet has achieved the one-shot tryout in more than 80% of cases”
Jyrki Hirvonen, Senior design engineer at Meconet.
4. One-shot tryout
Meconet has achieved a one-shot tryout in more than 80% of their cases. This is significant, as conducting trial-and-error loops is undoubtedly the most costly and time-consuming stage of the deep drawing process.
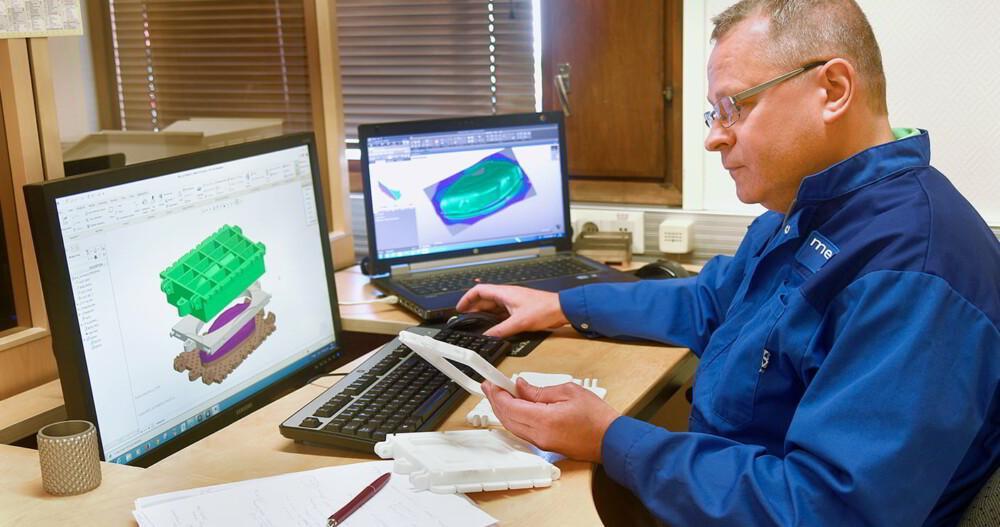
5. Sustainability
Many cost-saving initiatives also have a positive impact on sustainability. For example, Meconet optimized the sheet thickness for a customer’s parts, saving 15 kilograms of steel per product. They achieved this by optimizing the shape, sheet thickness, and using high-strength steel.
A kilogram of steel is equivalent to two kilograms of CO2 emissions, saving 30 kilograms of CO2 per product with this initiative. The weight savings significantly reduced the company’s carbon footprint, especially considering the high number of parts produced. This illustrates how simulation can contribute not only to cost savings but also to a company’s environmental targets by minimizing waste and CO2 emissions.
Conclusion
Simulation has become an integral part of Meconet’s deep drawing process. By simulating the entire process, they can proactively discuss and address part modifications, springback results, surface defects, and other issues with the customer. They also analyze process robustness for higher volume production, allowing them to anticipate outcomes long before physical parts are made. All these factors save the company cost, manpower, and time.
(This article is published originally in formingworld.com.)
Blog
Make use of our sustainable development expertise in your product design
Our business strategy is based on sustainable development. As regards our operations, the goal is to halve the carbon footprint by 2025 and achieve carbon neutrality by 2030 at the latest.
Read more