The range of applicable raw-materials for deep drawing is wide indeed. For example, stainless, coated and uncoated steel, aluminium, copper, and brass can be formed in various shapes using deep drawing.
The possibility of flexibly creating forms and designs for today’s architectural requirements using deep drawing is especially fascinating. Deep drawing allows smooth mass production of facade panels, since the same deep drawing tool can be utilised in the manufacture of the topography of each element. Panel perforations and delimitations can also be tailored using 3D laser cutting.
An advantage of the deep drawing technique is that the manufacturability, durability and design of facade elements, for example, can be ensured by 3D modelling already during the design and production process.
More than 5,000 3D sheet metal elements for shopping centre walls
In March, we were proud to announce that our sheet metal panels were chosen for the facade of the Mall of Tripla in Pasila: In co-operation with YIT and Arkkitehdit Soini & Horto Oy, we won the main prize in the design category at the Plootu Fennica 2018 sheet metal product design competition. Our submission was also elected the Sheet Metal Product of the Year.
Stefan Ochsner from Arkkitehdit Soini & Horto Oy, the Architect of the Mall of Tripla, has said that it was important to create a partly transparent facade that highlights the pulse of the shopping centre. Views from both inside and outside are filtered through the perforated 3D metal facade. At night, the dynamic lighting system further enhances the character of the facade. According to Ochsner, the objective was to create a strong, memorable identity for the shopping centre, and Meconet possessed the competitive technical manufacturing expertise required for production of the facade panels.
The shape of the facade panels for the Mall of Tripla is created using the deep drawing technique, by which twenty three ‘cups’ of different size are formed in the panel. After this, holes are made in the cups by 3D laser cutting. This is a truly novel, innovative facade solution, implemented by a method used relatively rarely in case of facades.
For the facade, we manufactured more than five thousand three-dimensional elements at the Meconet factory in Äänekoski. In addition to the facade elements, Meconet also developed the product manufacturing method and provided the necessary deep drawing tools.
High quality result through careful product development
Within the framework of this project, we utilised simulation and 3D printing already in the product development stage, thereby ensuring facade panel manufacturability, durability, and design. Choosing the right material was a major part of the product development. In case of the Mall of Tripla, decision was in favour of stainless steel characterized by excellent formability and usability characteristics.
Prior to choosing the material, the optimal manufacturing method for the facade panel desired was sought for during the concept stage. Based on designs by the Architect, the facade panel material and manufacturability were mapped by preliminary simulation and feasibility analysis.
In the beginning, there may be several concept alternatives. For manufacturing purposes, it is necessary to decide on the material and surface preparation technology used in the facade, and on whether the end product will be painted after deep drawing. Finding the correct raw material and surface was of primary importance, and careful mapping of the options took time.
After identifying the right concept, a physical prototype of the facade element was built during the prototype stage, which was tested and validated. The most “tangible” part of this was constructing a test wall, which is already visible to the passers-by at the Pasila temporary station. The test facade was used to verify year-round weather resistance of the facade to be built.
Practical validation also included simulations in the virtual environment and at our factory in Äänekoski. During the prototype stage, we made sure the wall could actually be built. For this purpose, we also 3D printed a model of the final product size!
After the prototype stage, the tools necessary for facade manufacture and other details were designed. After building of the deep drawing tool, it can be used for mass production of facade elements.
Our work is based on values
Our values are visible in this project as well: expertise, responsible attitude, and continuous improvement. Through utilisation of our technological expertise, we create added value for our customers and remain at the forefront of development. We act in a responsible manner, which means that everyone at Meconet is responsible for the achievement of our common goals. Continuous improvement allows enhancing our competitive ability, increasing job satisfaction, and creating added value.
Would you like to know more about the deep drawing technology? Order deep drawing tips directly to your Inbox!
Want to hear more about deep drawing technology? Download our guide!
Ask more about our services
Contact us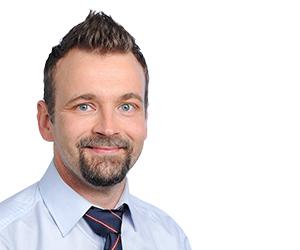
Tips: Product Design Opportunities Offered by Servo-controlled Deep Drawing
Do you have new products in mind? Or perhaps you would like to manufacture your current products more efficiently or comprehensively? Servo-controlled deep drawing may well be the answer. Download our guide and learn more about the possibilities offered by the technology.
Download tips