A common misunderstanding suggests that deep drawn products are expensive. According to our experience, for example, customers may be reluctant to introduce deep drawing technologies in their own processes, since they consider the required tool investments too costly. However, startled by the estimated cost of the initial investment, people often fail to take into account all of the positive multiplier effects resulting from deep drawing on the end products and especially on total costs.
Indeed, use of deep drawn components allows significant savings: smaller number of components, better dimensional accuracy, and reduced weight of the end product. Requirements to connectable parts are easier to meet, welding can be limited and the number of work stages reduced. When total costs are considered, the tool investments that seemed expensive at first can pay off in a very short time and the deep drawing technology actually allows cost saving.
Savings in costs and materials
By deep drawing, it may even be possible to get the finished product in a single production stage. We once manufactured a bottom pan for the engine of a work machine using the deep drawing method. Earlier, the same product had been welded together of 18 different pieces of metal, since the pan had to fit into limited space and accommodate various pipes. Thus, the task was quite complex. Using the deep drawing method, we manufactured the pan in a single piece, without any welds. This also meant a healthy weight loss for the pan, as well as extra space for the pipes.
Cavities can also be integrated into a single deep drawn form. For example, lock mechanisms and hinges can be embedded into hatches, which means that the total number of components in the overall structure can be reduced significantly. This brings cost savings as well, since each individual product component requires management.
Strength and quality
Deep drawn forms strengthen the structure by themselves, which means that material thickness can be reduced significantly. This is reflected in both the material costs and the weight of the end product – a thin product is also light.
In deep drawing, the sheet material is strengthened through forming. Forms can be used for inclusion of stiffeners in the product, which in turn increases product durability. The deep drawing technology significantly reduces the number of welds or allows avoiding them completely. Sheet metal product welding is often a slow stage and a raw process deteriorating both dimensional accuracy and finished product appearance.
Dimensional accuracy and beauty of form
If not before, the deep drawing tool proves its excellence in the stage of serial production. The components are dimensionally accurate and manufacturing process reproducibility excellent. The deep drawing technology also results in extremely smooth and high-quality product surface.
Furthermore, the deep drawing technology gives product designers almost unlimited possibilities for inventing visually striking and functional end products – but this is the subject of our next blog post.
Do you want to hear more about deep drawing? Download our guide!
Ask more about our services
Contact us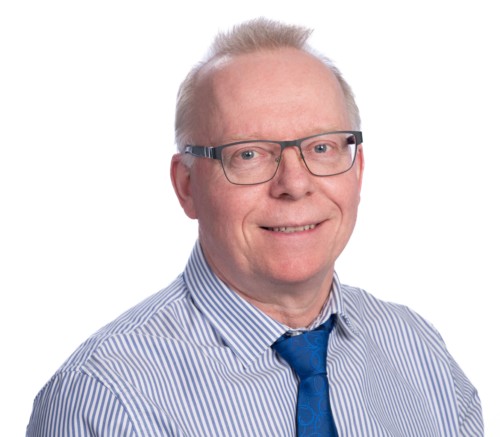
Tips: Product Design Opportunities Offered by Servo-controlled Deep Drawing
Download tips