
From the very start, Mitsubishi Logisnext Europe (MLE) has focused its business solely on electric forklifts. This decision turned out to be a successful one, as the technology in the forklift industry is developing towards fully electric operation. In 2013, MLE expanded its range to include larger counterbalance forklifts, and the first counterbalance forklift of their own design was brought to the market already in the following year.
Today, MLE manufactures approximately 5,000 counterbalance forklifts annually at its Järvenpää factory (formerly Rocla) and is among Europe’s largest players in the industry in terms of market share. Meconet supplies to MLE various deep-drawn components for both warehouse and counterbalance forklifts.
Design means co-operation
For MLE, product development co-operation with the suppliers plays a crucial role. The objective is always to develop forklifts that are not only efficient and durable, but also user-friendly and aesthetically appealing. This is manifested, for example, in MLE’s Evolt 48, a model that won the international Red Dot design award in 2019.
When a new forklift model is designed or an old one updated, the process starts from close dialogue with the suppliers. Meconet’s experts suggest ideas and options in the early stages of design that can optimise the manufacturing process and improve cost efficiency.
“The co-operation also included Meconet’s training courses where MLE’s designers were provided with information about new technologies and manufacturing possibilities.”
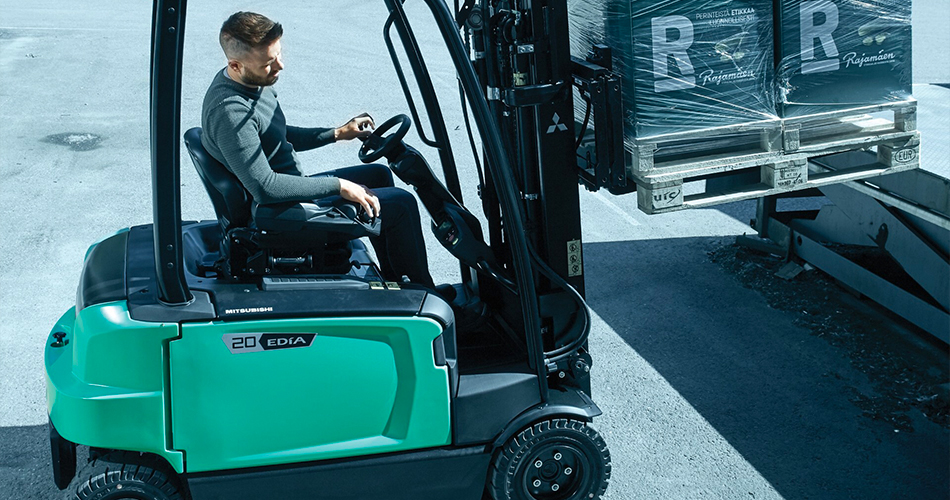
For example, in the design of forklift side panels, Meconet’s expertise related to deep drawing technology has been useful indeed. The co-operation also included Meconet’s training courses where MLE’s designers were provided with information about new technologies and manufacturing possibilities.
“Co-operation is a comprehensive package. It all starts with the design phase, during which we support the designers. In addition to the production of metal parts, Meconet is responsible for the entire manufacturing chain. The products are delivered complete with surface treatment and assembled (e.g., hinges, handles, locks) directly to MLE’s assembly line. In the final analysis, managing the entire supply chain is the core of this co-operation,” says Vesa Ovaska, the Account Manager for Meconet.
Quality, resilience and security of supply
MLE expects compliance with the TCO (Total Cost of Ownership) from all its suppliers – in other words, the best possible combination of price, quality, and technology. Also, the security of supply is very important. Component manufacture logistically near the assembly line is less risky and supports MLE’s goal of maintaining trouble-free business. For example, the partners have successfully solved the challenges related to availability of raw materials and components in a flexible manner.
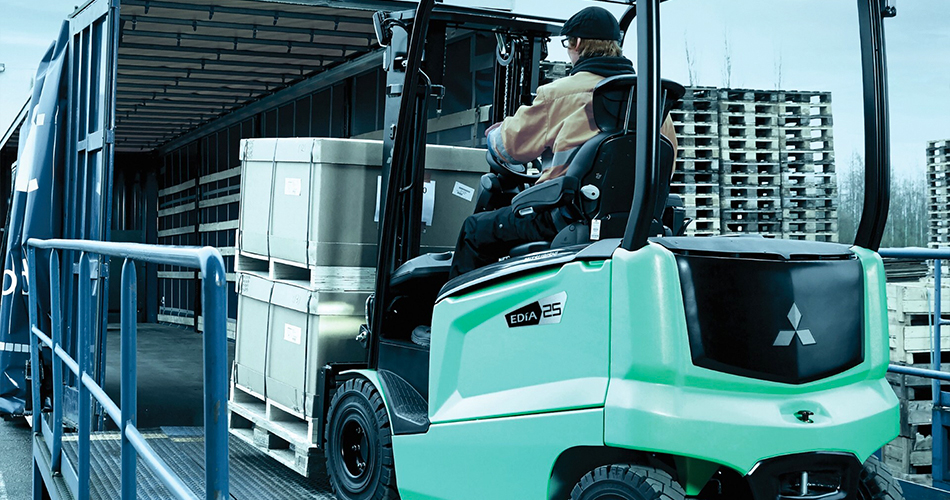
“Our long-term partnership is based on trust, joint development work, and the ability to meet the changing needs of the market”
Quality is also a critical factor. This holds especially true in case of painted outside components supplied by Meconet, as even the smallest of defects can lead to rejection of the goods.
“MLE and Meconet have co-operated for more than a decade. This long-term partnership is based on trust, joint development work, and the ability to meet the changing needs of the market,” says Simo Kangastupa, MLE’s Sourcing Director.
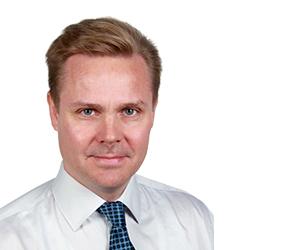
GUIDE: Consider these matters when designing e-Mobility products
Is your business related to e-Mobility? Do you have in mind any products intended for the electric mobility industry? We put together a guide for you on efficient and environmentally friendly design and production of e-Mobility products.
Read more