
Seit seiner Gründung hat sich Mitsubishi Logisnext Europe (MLE) ausschließlich auf Elektrogabelstapler konzentriert. Die Entscheidung erwies sich als erfolgreich, denn die Technologie im Bereich der Gabelstapler entwickelt sich in Richtung vollelektrisch. Im Jahr 2013 erweiterte MLE sein Sortiment um größere Gegengewichtsstapler und bereits im folgenden Jahr wurde das erste selbst konstruierte Gegengewichtsstaplermodell auf den Markt gebracht.
Heute stellt MLE in seinem Werk in Järvenpää (ehemals Rocla) jährlich rund 5.000 Gegengewichtsstapler her und ist gemessen am Marktanteil eines der größten Unternehmen der Branche in Europa. Meconet beliefert MLE mit mehreren Tiefziehteilen sowohl für Lager- als auch für Gegengewichtsstapler.
Planung ist Zusammenarbeit
Für MLE spielt die Produktentwicklungskooperation mit den Lieferanten eine entscheidende Rolle. Das Ziel ist immer, einen Gabelstapler zu entwickeln, der nicht nur effizient und langlebig, sondern auch benutzerfreundlich und ästhetisch ansprechend ist. Das zeigt sich zum Beispiel am Modell Evolt 48 von MLE, das 2019 mit dem internationalen Red Dot Design Award ausgezeichnet wurde.
Wenn ein neues Gabelstaplermodell entworfen oder ein altes aktualisiert wird, beginnt der Prozess mit einem engen Dialog mit den Lieferanten. In der frühen Phase der Planung bieten die Experten von Meconet Ideen und Alternativen an, mit denen sich der Herstellungsprozess und auch die Kosteneffizienz optimieren lassen.
„Die Zusammenarbeit umfasst auch Schulungen von Meconet, bei denen die Konstrukteure von MLE neue Technologien und Fertigungsmöglichkeiten kennenlernen.“
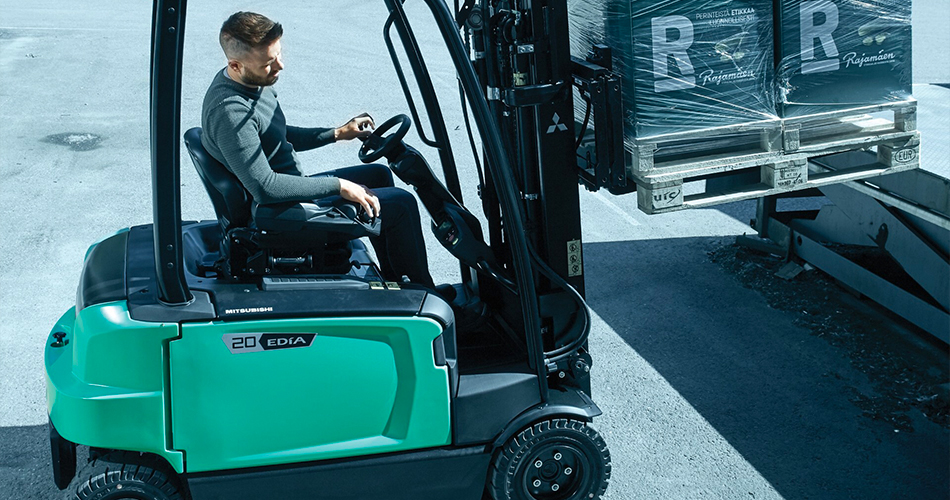
Das Know-how von Meconet in der Tiefziehtechnologie hat sich zum Beispiel bei der Konstruktion von Seitenplatten für Gabelstapler als nützlich erwiesen. Die Zusammenarbeit umfasst auch Schulungen von Meconet, bei denen die Konstrukteure von MLE neue Technologien und Fertigungsmöglichkeiten kennenlernen.
„Zusammenarbeit ist eine Gesamtheit. Alles beginnt mit der Planungsphase, in der wir die Konstrukteure von MLE unterstützen. Neben der kostengünstigen Herstellung von Metallteilen ist Meconet für die gesamte Fertigungskette verantwortlich, sodass die Produkte oberflächenbehandelt und zusammengebaut (z. B. Scharniere, Griffe, Schlösser) direkt an die Montagelinie von MLE geliefert werden. Letztendlich ist das Management der gesamten Lieferkette das Wichtigste in dieser Zusammenarbeit“, sagt Vesa Ovaska, Account Manager von Meconet.
Qualität, Belastbarkeit und Liefersicherheit
MLE erwartet von allen seinen Lieferanten, dass sie TCO (Total Cost of Ownership) umsetzen, das heißt dass Preis, Qualität und Technologie möglichst optimal abgestimmt werden. Der Vorteil der heimischen Produktion wird vor allem in Hinblick auf die Liefersicherheit hervorgehoben: In Finnland hergestellte Teile sind logistisch weniger riskant und unterstützen das Ziel von MLE, einen störungsfreien Betrieb aufrechtzuerhalten. So konnten zum Beispiel Herausforderungen in Zusammenhang mit der Verfügbarkeit von Rohstoffen und Komponenten gemeinsam flexibel gelöst werden.

„Die langfristige Partnerschaft basiert auf Vertrauen, gemeinsamer Entwicklung und der Fähigkeit, auf die sich ändernden Marktbedürfnisse zu reagieren.“
Auch die Qualität ist ein kritischer Faktor. Vor allem bei den lackierten Seitenteilen, die von Meconet geliefert werden, können schon kleine Fehler zur Ausschleusung des Stückes führen.
„MLE und Meconet arbeiten seit über einem Jahrzehnt zusammen. Diese langfristige Partnerschaft basiert auf Vertrauen, gemeinsamer Entwicklungsarbeit und der Fähigkeit, auf die sich ändernden Marktbedürfnisse zu reagieren“, sagt Simo Kangastupa, Einkaufsleiter bei MLE.
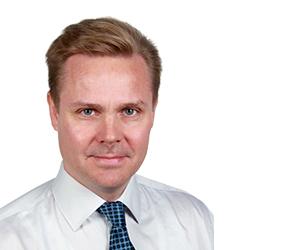
LEITFADEN: Berücksichtigen Sie diese Dinge bei der Entwicklung von Produkten für die E-Mobilität
Ist E-Mobilität Ihre Geschäftstätigkeit? Haben Sie vor, Produkte für die Elektromobilitätsbranche zu entwickeln? Wir haben für Sie einen Leitfaden für die effiziente und umweltfreundliche Planung und Produktion von Produkten für die E-Mobilität erstellt.
Mehr erfahren