The main task of a spring is to produce the force required for the operation of the end product. However, to operate, a spring requires enough space around it. The No. 1 challenge in spring design is often the lack of space reserved, which results in spending excessive time and resources on the design. The good news, however, is that this problem can be avoided by commencing spring design before finalizing everything else around the spring.
Consideration of the intended use and of the force required ensures functionality of the end product and prevents additional costs already at the design stage. These three issues should be taken into account in the design:
- In what kind of place the spring must fit?
- What kind of force is expected from a spring of certain dimensions?
- How will the spring be used? Will the spring be subjected to dynamic or static load?
Reserve enough space for spring
The most challenging aspect of spring design is when the spring must produce considerable force, but the space available is limited. In such cases, the spring wire is easily exposed to heavy and/or over stresses. Narrow space often poses a problem if the spring is used inside a cast metal or plastic component. If narrow space and the need for great force are combined with dynamic loading, spring manufacturing requires special operations.
The restrictions imposed by narrow space can be overcome by pre-stressing or using wires of higher tensile strength. However, as you might have guessed, this means higher costs in case of both manufacture and raw materials. As a rule of thumb, from the viewpoint of mechanics, modification of cast metal or plastic components is more sensible than manufacturing springs for spaces that are too tight.
Make sure the spring works in its environment
If a spring has been supported in some way (as it should be), it must be made sure that the spring co-operates seamlessly with the surrounding components. If a spring has been placed into a narrow space, tight tolerances are required with respect to dimensioning, which usually means increased manufacturing expenses.
I remember a case with a lock including a torsion spring supported on an axle at the centre of the spring body. Even though the spring produced the force required, the lock did not pass the durability tests. Having examined the end product in more detail, we discovered that the axle inside prevented the spring from turning further. The mechanical component forcefully bended the spring, which lead to breakage. The problem was resolved by making the axle thinner. Therefore, it is not enough for the spring to fit into an inactive product; it must be made sure that the spring does not collide with its environment.
Careful spring calculations prevent problems
Exceptionally often, the reason for spring breakage or quality loss is not readily evident for a layman and corrective product modifications need not be right. Nevertheless, even the most difficult spring challenges can be resolved in co-operation, through careful examination of the customer’s end product and spring calculations. In good mechanical design, for example, it is considered how the spring body of a torsion spring extends and the inner diameter reduces as the spring is turned and loaded. Or how the external diameter of a compression spring increases under pressure. These are some of the details that can be identified from Meconet’s spring calculations.
For us, the most important task in design is ensuring spring functionality in a single go, so that it meets our customer’s needs, endures and can be efficiently manufactured. However, we do not need to know everything in advance, since it is our task to support our customers at the various stages of the design process.
Do you want to hear more about spring design? Download our guide!
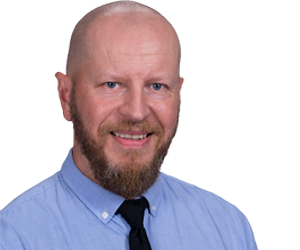
Download spring design tips
Download tips