Meconet ist ein nordeuropäischer Hersteller hochwertiger Tiefziehplatten für forstwirtschaftliche Erntefahrzeuge, Geländefahrzeuge und verschiedene andere Anwendungen und beliefert Kunden wie AGCO, John Deere und Mitsubishi Logisnext. Das Unternehmen stellt die Werkzeuge bereit, die diese Erstausrüster zum Tiefziehen zuverlässiger Blechteile benötigen.
Meconet hält an seinem Motto „Innovations are built together“ fest, indem es während des gesamten Prozesses eng mit den Kunden zusammenarbeitet, von der Planung bis zur Serienproduktion. Simulation spielt eine Schlüsselrolle bei der Unterstützung der Werkzeugkonstruktion und -analyse zum Erreichen der Ziele.
Simulation bei Meconet: Eine historische Perspektive
Vor zwei Jahrzehnten folgte Meconet den Branchennormen und verließ sich bei der Entwicklung hochwertiger Werkzeuge auf das Fachwissen von Experten im Tiefziehen. Es wurde ein grundlegendes Design entwickelt und dieses schrittweise durch das Prinzip von Versuch und Irrtum verbessert. Dieser Prozess war zeitaufwändig und kostspielig und erforderte erhebliche Ressourcen, um zufriedenstellende Ergebnisse zu erzielen.
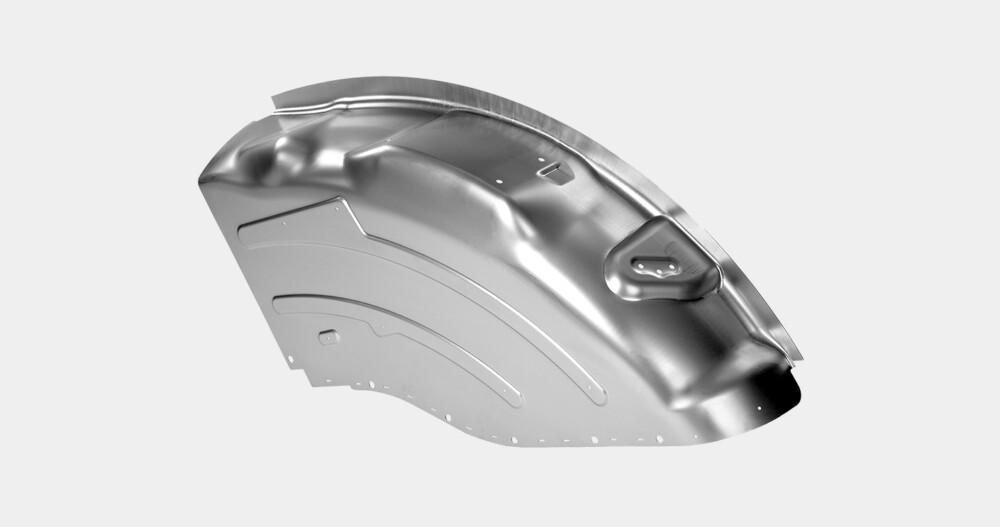
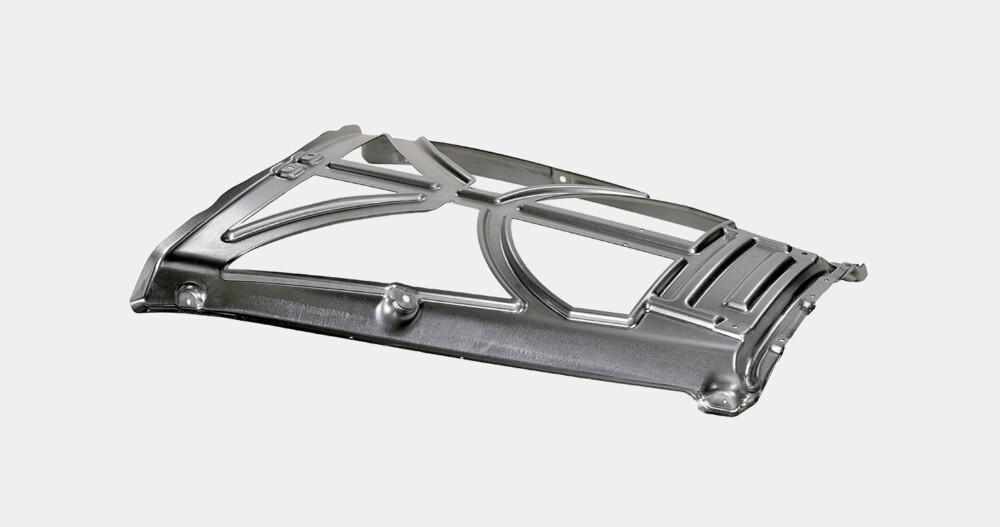
Diese Methode änderte sich im Jahr 2004, als Meconet begann, eine Tiefziehsimulationssoftware einzusetzen, um die Qualität und Effizienz seiner Tiefziehwerkzeuge zu verbessern. Es war eines der ersten Unternehmen außerhalb der Automobilindustrie, das mit der Tiefziehsimulation experimentierte. Heute arbeitet Meconet vom Teiledesign bis zur Installation eng mit seinen Kunden zusammen und stellt so die überlegene Qualität seiner Tiefziehteile sicher.
„Simulation ist heute ein wesentlicher Bestandteil des Prozesses bei Meconet“
Juho Pirnes, technischer Leiter und Manager der Markteinführung bei Meconet
Die Rolle der Simulation bei Meconet
Die Simulation ist nun ein wesentlicher Bestandteil von Meconets Prozess. Es wird mit der Beurteilung der Machbarkeit der Ausrichtung des Designs des Kunden an seinen gewünschten Zielen begonnen. Wenn der Kunde zum Beispiel den Teil mit nur einem Werkzeug tiefziehen möchte, analysieren die Ingenieure von Meconet das Design und arbeiten mit dem Kunden zusammen, um sicherzustellen, dass ein einziges Werkzeug den gesamten Teil Tiefziehen kann.
Gemäß dem Motto des Unternehmens, „Innovations are built together“, arbeiten die Planungs- und Testteams von Meconet eng untereinander und mit dem Kunden zusammen. Dieser kollaborative Ansatz bricht die üblichen Bunker auf und sorgt für einen gut konzipierten Prozess, der innerhalb des vorgegebenen Zeitrahmens qualitativ hochwertige Teile liefert. Derzeit nutzt das Unternehmen Simulationen für das Tiefziehen von Aluminium, Schnellarbeitsstahl und Edelstahl.
Meconet bietet umfassende interne Fertigkeiten, darunter Blechschneiden, Tiefziehen, 3D-Laserschneiden, mechanisches Schneiden, Waschen, Roboterschweißen und Nietarbeiten. Es werden Simulationswerkzeuge für Teile unterschiedlicher Größe verwendet, von kleinen Bauteilen bis hin zu sehr großen Tiefziehteilen mit 3000 mm.
Vorteile der Simulationsintegration
Die Simulation spielte eine entscheidende Rolle dabei, dass Meconet zahlreiche Ausschreibungen gewann und konsistent die Fristen der Kunden einhielt oder übertraf. Zu den spezifischen Vorteilen gehören:
1. Ein Komplettanbieter für alle Tiefziehbedürfnisse
Die Kunden haben jetzt einen einzigen Partner, der sie während des gesamten Vorgangs unterstützt, von der Planung bis zur Serienproduktion. Meconet hilft beim Entwerfen von Werkzeugen basierend auf der Teilegeometrie, bei der Zusammenarbeit bei Änderungen und bei der Gestaltung des Prozesses und der Werkzeuge. Die Werkzeuge werden dann in der Produktion von Meconet installiert, um ein nahtloses Kundenerlebnis zu gewährleisten.
2. Reduzierte Werkzeugkosten
Natürlich möchten die Kunden die Anzahl der Werkzeuge minimieren, die zur Herstellung des Endprodukts aus dem Rohling erforderlich sind, um Kosten zu sparen, insbesondere bei der Produktion kleiner und mittlerer Stückzahlen. Außerdem möchte man nach Möglichkeit die Anzahl der Teile bei gleichbleibender Funktion minimieren. Dadurch entfallen auch zusätzliche Prozesse wie das Schweißen und die Montage wird vereinfacht.
Durch die Simulation kann sich Meconet in diesem Bereich im Vergleich zu seinen Konkurrenten hervortun, indem es mehrere Teile zu einem einzigen Tiefziehteil zusammenfasst, der auch mit einem einzigen Werkzeug gestanzt werden kann. Dadurch wird die Produktion bis zur Phase der Ziehmatrize optimiert, gefolgt vom Lasertrimmen für einen fertigen Teil.
In einem Fall reduzierte Meconet die Anzahl der Teile für einen französischen Kunden von sieben auf nur einen. Der Kunde ist seitdem ein Stammkunde von Meconet.
3. Vorteile des Laserschneidens
Während das Laserschneiden in der Automobilindustrie aufgrund der hohen Stückzahlen möglicherweise nicht so kosteneffizient ist, kann es in industriellen Anwendungen mit geringeren Stückzahlen effektiv eingesetzt werden. Meconet integriert das Laserschneiden effektiv in seine Prozesse, da die Anzahl der Teile und das Gesamtproduktionsvolumen reduziert sind. Es kann jede benötigte Form programmiert, fixiert und mit dem Laser zugeschnitten werden, sodass nur ein einziger Laserschnitt erforderlich ist, um nach der Phase der Ziehmatrize den endgültigen Teil zu erhalten.
Meconet hat die One-Shot-Probe in mehr als 80 % der Fälle bestanden“
Jyrki Hirvonen, leitender Designingenieur bei Meconet
4. One-Shot-Probe
Meconet hat die One-Shot-Probe in mehr als 80 % der Fälle bestanden. Dies ist von Bedeutung, da die Durchführung von Versuch-und-Irrtum-Schleifen zweifellos der kostspieligste und zeitaufwändigste Schritt des Tiefziehprozesses ist.
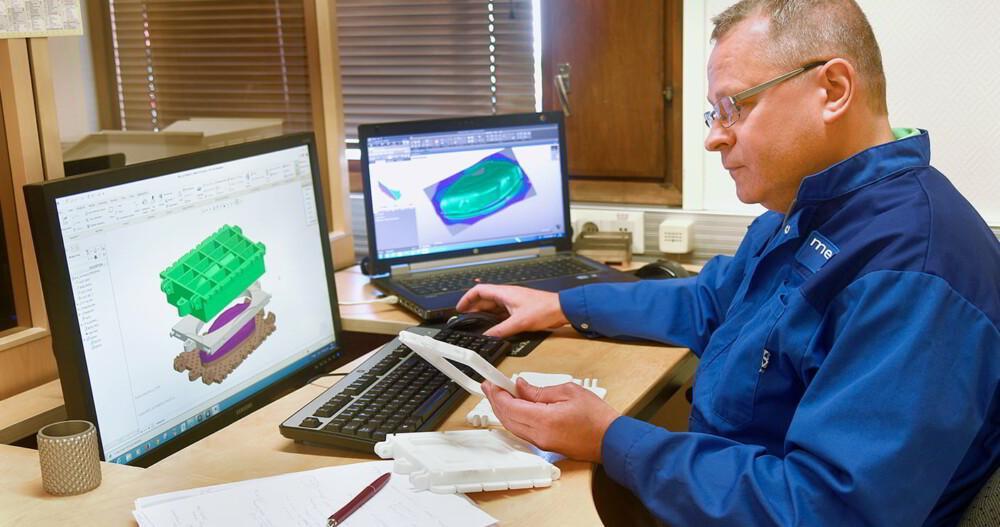
5. Nachhaltigkeit
Viele kostensparende Initiativen wirken sich auch positiv auf die Nachhaltigkeit aus. Zum Beispiel optimierte Meconet die Blechdicke für die Teile eines Kunden und sparte dadurch 15 Kilogramm Stahl pro Produkt. Dies wurde durch die Optimierung der Form, der Blechdicke und den Einsatz von hochfestem Stahl erreicht.
Ein Kilogramm Stahl entspricht zwei Kilogramm CO2-Emissionen, wodurch mit dieser Initiative 30 Kilogramm CO2 pro Produkt eingespart werden. Die Gewichtseinsparungen reduzierten den CO2-Fußabdruck des Unternehmens erheblich, insbesondere angesichts der hohen Anzahl produzierter Teile. Dies verdeutlicht, wie Simulation nicht nur zu Kosteneinsparungen, sondern auch zu den Umweltzielen eines Unternehmens beitragen kann, indem sie Abfall und CO2-Emissionen minimiert.
Fazit
Die Simulation ist zu einem integralen Bestandteil des Tiefziehprozesses von Meconet geworden. Durch die Simulation des gesamten Prozesses können proaktiv Teileänderungen, Rückfederungsergebnisse, Oberflächenfehler und andere Probleme mit dem Kunden besprochen und behoben werden. Es wird auch die Prozessrobustheit für die Produktion größerer Stückzahlen analysiert und somit werden Auswirkungen vorhergesehen, lange bevor physische Teile hergestellt werden. All diese Faktoren sparen dem Unternehmen Kosten, Arbeitskraft und Zeit.
(Dieser Artikel wurde ursprünglich auf formingworld.com veröffentlicht.)
Blogs
Nutzen Sie unser Fachwissen in der nachhaltigen Entwicklung in Ihrer Produktplanung
Unsere Geschäftsstrategie basiert auf nachhaltiger Entwicklung. In Bezug auf unseren eigenen Betrieb ist es unser Ziel, unseren CO2-Fußabdruck bis 2025 zu halbieren und bis spätestens 2030 CO2-Neutralität zu erreichen.
Lesen Sie mehr