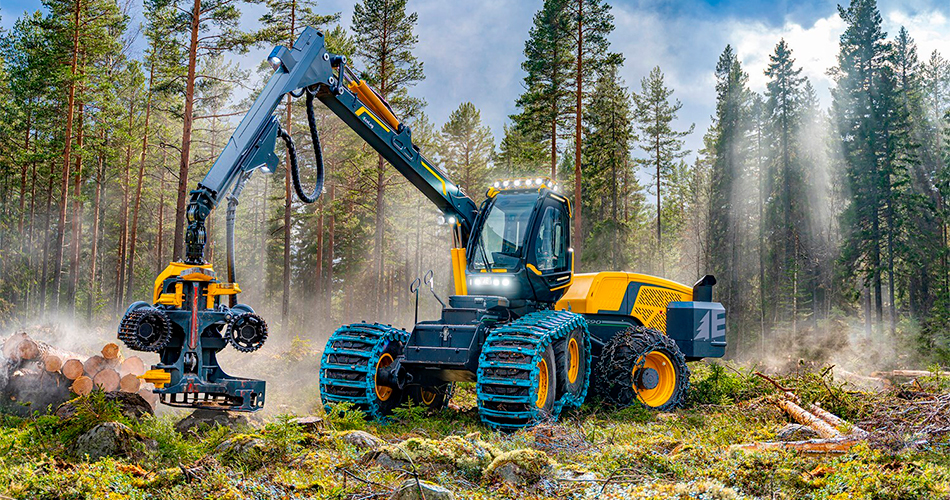
Eco Log manufactures and sells efficient and highly productive forest machines for sustainable forestry.
The new G series harvesters by Eco Log are equipped with a completely new, modern and spacious cab, where every detail is carefully selected. An essential part is the design and styling of the cab, which also affects the user experience and comfort. The cab is the harvester operator’s office where their entire workday is spent. This is why comfort is paramount.
A servo-controlled deep drawing line has many benefits
Meconet supplies the new G series cabs with deep-drawn body parts, which offer a number of advantages over previous cabs. There are a total of 10 deep-drawn parts in the cab.
“The modern shapes of the cab are formed by Meconet’s new, servo-controlled deep-drawing line.”
The new cabin takes its design inspiration from the automotive industry. The modern shapes of the cab are formed by Meconet’s new, servo-controlled deep-drawing line, which adds a designer touch – with very little welding required. The innovative use of deep-drawn cab components has made it possible to create uniform sub-assemblies in the design language of the cab which can be assembled efficiently with optimized frame structures, for example, in the cab door structure.
According to Markus Jouppila, the head of cab technology at Fortaco, the deep-drawn parts which were the design starting point for the cab allowed for a level of manufacturing precision that would not have been achieved with traditional solutions. A good example is a door with a frame made from a few pieces with little welding. The deep-drawing design language also allowed for hidden hinges and ample storage space, which could now be added, unlike in cabs made using traditional methods.
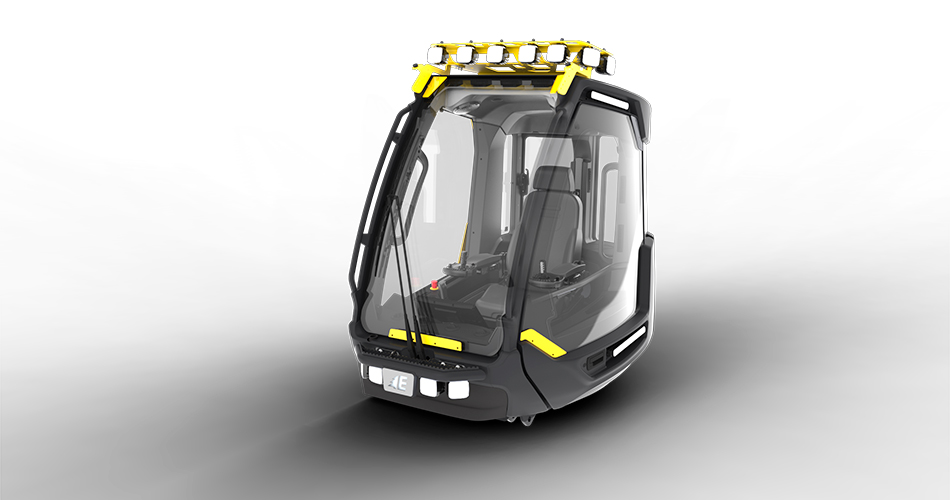
In addition to storage space, the double-curved shapes allowed for excellent visibility despite the large cab. It was possible to design driver ergonomics without having to compromise, and traditional screws and welds are nowhere to be seen in the cab.
”As much as 80% of the costs are determined at the product and tool design stage.”
Cooperation starts from the design stage – impacts the carbon footprint as well
In addition to the actual production of parts, cooperation with both Eco Log and the cab manufacturer Fortaco covers much of the production chain. Meconet was already involved to support the design phase. To make full use of the new servo-controlled deep drawing press, early cooperation is essential. As much as 80% of the costs are determined at the product and tool design stage. Involvement in the design has helped minimise tool investments and the number of parts and work stages, reducing the carbon footprint of both Meconet and the customer.
– With Meconet’s modern digital tools and production equipment, we have achieved significant benefits. The innovation work started with the customer at the early stages is also reflected in the end result, in terms of product functionality and total cost, for example,” says Juho Pirnes from Meconet.
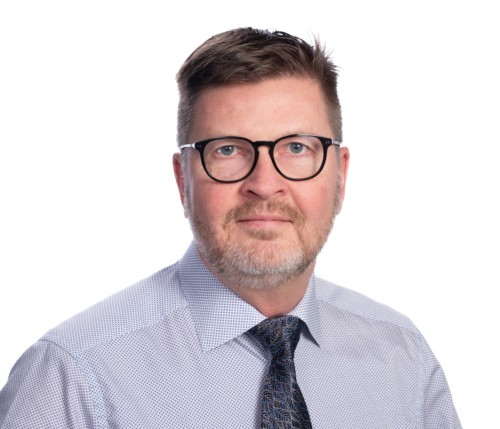
GUIDE: Consider these matters when designing e-Mobility products
Is your business related to e-Mobility? Do you have in mind any products intended for the electric mobility industry? We put together a guide for you on efficient and environmentally friendly design and production of e-Mobility products.
Read more