Bei der Federkonstruktion und -fertigung arbeiten wir eng mit dem Kunden zusammen, um das bestmögliche Ergebnis für ihn zu erzielen. Das ist natürlich etwas, das wir immer anstreben, aber ich dachte, jetzt insbesondere über die Herausforderungen an die Federkonstruktion in der Waffenproduktion zu schreiben. Diese Produkte werden normalerweise für Freizeit-, Wettbewerbs- oder staatliche Zwecke verwendet, daher müssen sie vor allem sicher und zuverlässig sein. Die Ausgangspunkte für alles sind Produktsicherheit und Zuverlässigkeit.
Enorme Belastung einer Feder in einer Waffe
Typischerweise sind Waffen wertvoll und langlebig, mit einer Lebensdauer von oft mehreren Jahrzehnten. Das stellt die Feder vor Herausforderungen. Bei Waffen können die Mechanismen sehr herausfordernd und kritisch für das Endprodukt sein.
Eine komprimierte Feder wird typischerweise einer Belastung ausgesetzt, der die Feder mehrere Jahre lang standhalten muss. Die Anzahl der Wiederholungen kann enorm sein, und diese Belastung muss bei der Konstruktion der Waffenfeder auf unterschiedliche Weise berücksichtigt werden. Außerdem können Bewegungen mit der Waffenfeder sehr schnell sein. Waffenmechanismen erfordern im Allgemeinen auch mehrere Federn, die zusammenarbeiten. Es reicht zum Beispiel nicht aus, die Toleranzen nur einer Feder zu prüfen: Stattdessen müssen breitere Toleranzketten berücksichtigt werden, die aus anderen Federn und den umgebenden Teilen bestehen. Die Beherrschung dieser Toleranzketten erfordert einen möglichst präzisen Fertigungsprozess.
Bei Waffen ist die Verwendbarkeit eines Produktes mindestens genauso entscheidend wie die Toleranzketten. Beim Abfeuern einer Waffe wird immer Druck erzeugt. Damit eine Waffe dem standhält, muss sie aus hochwertigem Stahl gefertigt sein. Aus Gewichtsgründen wird jedoch die Stahlmenge minimiert, wodurch der für die Feder reservierte Raum typischerweise klein und eng ist. Daher muss die Feder über ihre gesamte Lebensdauer hinweg auf kleinstem Raum ihrem Einsatzzweck entsprechend arbeiten können.
Eine hochwertige Feder wird sorgfältig konstruiert und gefertigt
Wir verfügen über das nötige Know-how und die Methoden, um auch den anspruchsvollsten Federanforderungen gerecht zu werden. Durch das Vorspannen können wir die Streckgrenze des Federdrahtes und relevante Federeigenschaften erhöhen, sodass die Feder auch auf engstem Raum haltbarer ist. Mit dem Kugelstrahlen können wir die gewünschte Spannung über die gesamte Oberfläche der Feder erzielen und Mängel wie Kratzer beseitigen, die der wahrscheinlichste Ausgangspunkt für eine Beeinträchtigung der Funktion der Feder wären. Dieses Verfahren verbessert die dynamische Haltbarkeit der Feder erheblich.
Bei Meconet verfügen die Automatisierungslinien für die Schraubenfedern über eine mit Kameras umgesetzte Präzision von 100 %. So werden nur die besten Federn hergestellt. Federkonstrukteure müssen erfahren sein und möglichst effektive theoretische Berechnungsergebnisse erzielen. Eine hochwertige Fertigung vertuscht keine Konstruktionsfehler.
Eine Handfeuerwaffe wird während ihrer Lebensdauer typischerweise 15.000 – 20.000 Arbeitszyklen ausgesetzt. Beim Gebrauch beginnt sich die Feder zu verkürzen und verliert mit der Zeit an Kraft. Nach einer gewissen Zeit wird die Feder so locker, dass die Waffe nicht mehr schießen kann. Diese Eigenschaft kann der Feder nicht entzogen, aber durch gutes Design minimiert werden – im besten Fall ist der Effekt für das Endprodukt unbedeutend. Wenn der Konstruktions- und Herstellungsprozess gut abgeschlossen ist, funktionieren die Federn und das Endprodukt so lange wie möglich in der gewünschten Weise.
Kundenerwartungen übertroffen
Vor einigen Jahren wurden wir von einem Pistolenhersteller angesprochen, der gerade dabei war, zwei neue Pistolenmodelle zu entwerfen. Beide Modelle erforderten zwei Federn, und der vorherige Federhersteller hatte eindeutig Schwierigkeiten dabei, Konstruktion und Funktionalität von ausreichender Qualität zu bieten. Die Anforderungen an Qualität und Funktionalität wurden nicht erfüllt. Dies war der Ausgangspunkt für die Zusammenarbeit von Meconet mit dem Kunden.
Zunächst definierte der Kunde die erforderliche Funktionalität sowie den Platz und die Umgebung dieser beiden Federn in der Waffe. Der Kunde hatte kompetente Vertreter im Konstruktionsprozess und wir konnten Informationen und Grenzwerte zur Funktionalität einholen, um Federberechnungen und Simulationen schnell durchführen zu können.
Nach der ersten Phase war unser Federdesign bereits fertig und wir gingen in die Prototypenphase über. Nach einigen Prototypen gelang es uns, Federn für zwei Pistolen herzustellen, die alle Erwartungen des Kunden übertrafen. Nun gehen die Pistolen in die Phase der Serienproduktion über und der Kunde geht davon aus, dass diese neuen Produkte gut auf dem Markt ankommen werden.
Dieses Projekt war eine großartige Übung für den Kunden und für Meconet, da beide Parteien ihre Fachkenntnisse einbringen konnten, um ein Ergebnis zu erzielen, das unabhängig voneinander nicht erreichbar gewesen wäre. Die beste Art der Zusammenarbeit – innovations are built together!
Möchten Sie mehr über die Federkonstruktion erfahren? Laden Sie sich unseren Leitfaden herunter!
Fragen Sie mehr nach unseren Lösungen
Kontaktiere Sie uns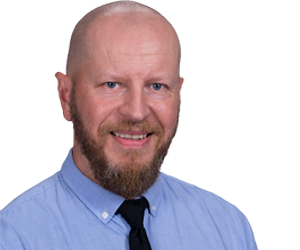